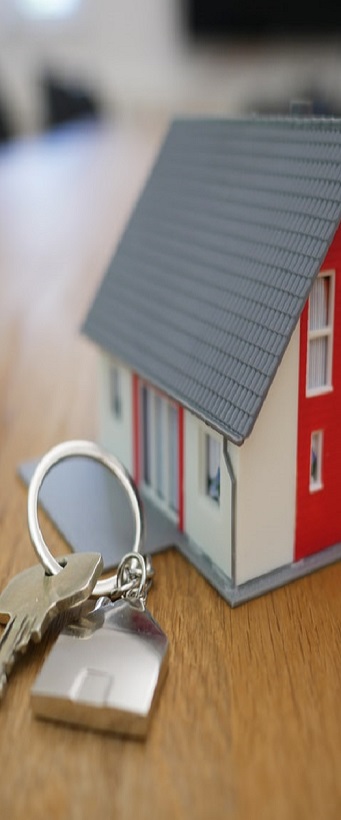 | In order to ensure that the servicing and repairs are being carried out correctly and in accordance with the contract we can provide Maintenance Audits which allow for the Lift Maintenance to be graded and to provide KPI’s on performance of the lift company for review.
On receipt of the relevant certification we can also monitor Loler items are being completed by the maintenance contractor.
If the equipment is on contract administration with LCG we would already manage the Loler process however if we are just completing an audit we would report back the findings to our clients if there were any issues found in relation to Loler items outstanding.
As well as collecting data on the standard or the maintenance we also look at the age, condition and usage of the equipment with a view of lifecycle replacement based on CIBSE guidelines.
By carry out contract administration of the installations and gathering the relevant information, such as call outs, changes of usage within the building and the level of maintenance in place, we can provide reports enabling us to identify trends which may affect the lifts performance and reliability.
The maintenance audit approach is to collect information from your current maintenance processes and from the information systems provided we can analyse them in order to suggest improvements and in some cases cost savings to your service going forward.
This could provide vital information that may improve your installation, the reliability of the lift or to improve the way your current maintenance company is addressing the maintenance on your behalf.
Our maintenance audit reports are easy to read and understand using a scoring system as a percentage and a RAG rating for the condition of the 10 main aspects of the installation.
GREEN:
Items that score highly would be green and deemed to be well maintained and in good condition.
AMBER:
Items in the mid-range would fall into this category. These would be deemed as poorly maintained, approaching the end of life or the component is not functioning correctly but is not a safety risk. i.e. Dirty Pit or car top.
RED:
Items that fall into the red category are either very poorly maintained, failure is very likely due to age and condition. The parts may be obsolete and are at risk of longer downtime when they fail, or the item is a safety concern to the users.
The full report when generated will then also provide an overall rating using the traffic light system.
GREEN:
Assets in this category can be considered as suitably satisfactory and without forfeiting any critical component of support.
AMBER:
Assets in this category have reached a steady state of decline and are approaching end of life expectancy or require attention by the incumbent service provider.
RED:
Assets in this category are deemed as either past their life expectancy cycle or require immediate attention by the incumbent service provider. The latter if addressed will then escalate into one of the two sections above, along with removing the probability of greater damage.
KPI’s
Part of our contract administration support is to focus and report on the key performance indicators that are important to each client.
These are agreed at the start of the contract and added to the maintenance tenders to make sure what is important to you is included and monitored for the duration of the maintenance contract. These can be on a variety of things such as.
• Response times.
• Completion of maintenance visits within set timescales.
• Number of calls in a set period.
• First time fixes.
• Minimum length maintenance times etc.
If you feel that your lift, escalator, stairlift, or goods lift could benefit from an audit, please do not hesitate to contact one of our team members on service@lcglifts.co.uk , or alternatively on our telephone number 02083201100.
| | |